The Snell M2015 Standard
October 10, 2014 (Press release edited by webBikeWorld.com)
The M2015 motorcycle helmet safety standard, known as the Snell standard for “Protective Headgear For Use With Motorcycles and Other Motorized Vehicles” has been published by the Snell Memorial Foundation.
The Snell laboratory is now accepting submissions for helmet certification to the M2015 standard.
Snell released the initial draft of the M2015 standard back in April of 2013 and the final version has quietly come to pass with final publication of the standard in Spring of 2014, but with little fanfare and no national press release.
The Bell Moto-9 Flex (Preview) is one of the first helmets to be announced that meets the Snell M2015 standard.
The following information was edited from the Snell M2015 standard information page on the Snell Memorial Foundation website.
We edited the versions of the Snell M2015 introductory explanation and below that is a copy of the Snell M2015 standard, displayed in an easy-to-read format.
For more information and any latest changes to the standard, be sure to visit the Snell Memorial Foundation website.
Also, here is an .mp4 video describing the new Snell M2015 standard.
Difference Between Snell M2015 and M2010
Enforcement Testing
The Snell M2015 standard is almost identical to Snell M2010 (report), but there is an important difference in the enforcement testing.
When samples of previously certified helmets are tested for compliance, the impact testing will be at the same impact velocities and to the same criteria prescribed for initial certification testing.
If a failure is observed, three more samples will be tested at slightly lower “deviation” velocities but the test criteria will be the same as those set for certification testing
The requirements also demand a new “Certification ID#” label in each certified helmet, specifying the original test series on which the certification is based.
This Certification ID# consists of two alpha characters followed by four digits, a hyphen and two more digits. It identifies the test lab, record number and year of the certification.
It may be found in the lower right corner of the certificate awarded when certification was granted.
This test series information is essential to determining the correct test set up parameters for enforcement testing and for reference to the helmet sample from the original set maintained in the Foundation’s helmet archive.
If the helmet owner can demonstrate that his products are reasonably identifiable without such labels, the Foundation may agree to waive this requirement. Any such waiver must be obtained in writing.
Modifications to Retention Strength and Shell Penetration Test Procedures
Other changes include modifications to the retention strength and shell penetration test procedures.
These changes will improve test reliability and repeatability but are not expected to materially affect test outcomes.
Timeline for M2015 Implementation
Certification Testing begins immediately. Note: M2010 certified models intended for the M2015 program must be submitted for separate M2015 certification testing.
M2015 Certification labels first available for shipment on April 1, 2014. M2015 labeled helmet units must not be available for sale or use before October 1, 2014.
Helmet models certified to M2015 are held to meet the requirements of M2010 and will be included in the M2010 program upon request.
As long as no claims of M2015 qualification are made, such units may be marketed with M2010 certification labels, M2010 markings and M2010 claims for the duration of the M2010 program.
Timeline for Snell M2010 shutdown. M2010 Certification Testing ends immediately. M2010 labels will be available through July 1, 2014. M2010 labeled production must cease March 31, 2015.
Details of the Snell M2015 Standard
Snell lists four reasons why motorcyclists should be interested in the new M2015 standard:
- The use of motorcycles and other motorized vehicles imposes risks of death or permanent impairment due to head injury.
- The proper use of protective helmets can minimize the risk of death or permanent impairment.
- The protective capacity of a helmet is difficult to estimate, particularly at the time of purchase or use. Protective capability is currently measured by destructive testing, which is beyond the means of most helmet wearers.
- Snell certification backed by ongoing destructive testing samples taken randomly from dealers and distributors identifies those helmet models providing and maintaining the highest levels of head protection.
Four of the most critical elements affecting a helmet’s protective properties are:
- Impact Management: how well the helmet protects against collisions with large objects.
- Helmet Positional Stability: whether the helmet will be in place, on the head, when it’s needed.
- Retention System Strength: whether the chin straps are sufficiently strong to hold the helmet throughout a head impact.
- Extent of Protection: the area of the head protected by the helmet.
Finding the Correct Fit for a Motorcycle Helmet
Following is a set of annotated and edited (by webBikeWorld) notes of a Snell press release that describes the M2015 standard and other recommendations for motorcycle helmet use.
Note that most of the recommendations are also the criteria that are detailed in thewebBikeWorld Motorcycle Helmet Reviews.
The M2015 standard describes simple tests for all four of these items.
However, the tests for the second item, helmet stability, of necessity presume that the helmet is well matched to the wearer’s head and that it has been carefully adjusted to obtain the best fit possible.
Unless you take similar care in the selection and fitting of your own helmet, you may not obtain the level of protection that current headgear can provide.
(More information on choosing the right motorcycle helmet in the webBikeWorld Motorcycle Helmet FAQ page. Also refer to the Motorcycle Helmet Shapes page for a list of helmet reviews by internal shape.)
The Snell Memorial Foundation recommends the simple, straightforward procedure recommended to consumers by most helmet manufacturers:
- Position the helmet on your head so that it sits low on your forehead; if you can’t see the edge of the brim at the extreme upper range of your vision, the helmet is probably out of place.
- Adjust the retention system so that when in use, it will hold the helmet firmly in place. This positioning and adjusting should be repeated to obtain the very best result possible. The procedure initially may be time consuming; take the time.
- Try to remove the helmet without undoing the retention system closures. If the helmet comes off or shifts over your eyes, readjust and try again. If no adjustment seems to work, this helmet is not for you; try another.
This procedure is also the basis of the test for helmet stability described in this Standard.
This test performs the same steps but uses standard head forms; however, you must still perform this procedure for yourself when buying a helmet and every time you wear a helmet.
Only in this way will you be able to make all the proper adjustments to get the best fit possible.
Furthermore, your test on your own head will be an improvement on ours; you will determine whether the helmet is appropriate for you personally.
There are several other important aspects of helmets to consider: full-face helmets provide a measure of protection from facial injuries.
These helmets incorporate a rigid chin guard which covers the lower part of the face. The Snell Memorial Foundation has devised special tests for the chin bars of full face helmets.
The Two Types of Full-Face Helmets
There are two varieties of full face helmets.The chin guard may be an integral, immovable part of the helmet but, in so-called “modular” or “flip-up” helmets the chin guard may be hinged so that, when released, it will pivot or flip up and out of the way for the rider’s convenience.
Modular helmets must meet all the same requirements as those equipped with integral chin bars, with the additional requirement that the chin guard release mechanism must be sufficiently secure to prevent inadvertent opening in a crash impact.
Helmets With Removable Chin Bars
Some helmets come with a separate structure which bolts to the helmet and which is intended to cover the lower part of the face.
These removable chin bars are often intended to deflect small stones and debris encountered in some motorcycle sports and may not be effective facial protection in falls and accidents.
It’s interesting to note that Snell states that they do “not test bolt-on chin bars and considers any headgear equipped with them to be an open face helmet.”
This is curious, as there doesn’t seem to be any technical reason why a helmet with a secure removable chin bar or guard can’t be made as strong or secure (or more) than a flip-up helmet, many of which have very poor rotating flip-up visor retention systems, as noted in the webBikeWorld Motorcycle Helmet Reviews.
Face Shield
If a full face helmet is equipped with a face shield, it may also provide a measure of eye protection. The Foundation tests the face shields of full face helmets for particle penetration resistance.
Face shields provided with open face helmets generally do not provide the same levels of eye protection and, for that reason are not considered.
The shells of both open and full face helmets should also provide a measure of protection from penetration. The Foundation tests the shells of both full and open face helmets for penetration resistance.
Emergency Removal
Effective headgear must be removable; paramedics and other emergency personnel must be able to quickly remove headgear from accident victims in order to check for vital signs and to perform emergency procedures.
The Foundation has devised tests and criteria for helmet removability.
Outward Visibility
The Foundation tests helmets for visual field. The helmet must provide a minimum range of vision appropriate to its use as measured on standard head forms.
Most Snell certified helmets will meet the requirements stated in this Standard and are considered appropriate for street use.
However, the Foundation may also certify headgear with much more restricted visual fields for use only in carefully controlled competitive environments.
Such headgear will include warning labels identifying them as appropriate only for certain activities.
Be absolutely certain that your helmet is appropriate for your intended uses. Furthermore, since the range of vision you obtain may vary considerably from our measurement, be absolutely certain that the helmet and face shield permit you adequate vision.
There are several important factors which the Foundation does not consider directly but which bear on the effectiveness of protective helmets.
Be certain your helmet is wearable, that is, that it’s comfortable and adequately ventilated when worn for prolonged periods (matching your head shape to the helmet’s internal shape is crucial; see the webBikeWorld Motorcycle Helmet FAQ page and the Motorcycle Helmet Shapespage for more information).
Few people will wear an uncomfortable helmet and a helmet that is not worn won’t protect.
Also, while you’re trying the helmet on, take a good look in a mirror and ask some friends what they think. Most people will quit using an ugly helmet much more quickly than one that is merely uncomfortable.
Helmet Conspicuity
Check for conspicuity. Bright colors and reflective patches will make you more visible to others and therefore less likely to be involved in a collision. All your riding gear and especially your helmet should be unmistakable, even to the most inattentive driver.
The Snell M2015 Standard
Following is an edited version of the entire Snell M2015 motorcycle helmet safety standard, annotated and edited by webBikeWorld.
For more information and the exact details of the standard, along with a list of Snell certified helmets, refer to the Snell Memorial Foundation website.
Background
In a motorcycle accident, the rider may suffer injury or death. Helmets on the market today offer varying degrees of protection, but the consumer has little basis for judging the relative effectiveness of a given model.
This Standard presents rational methods for identifying those helmet models which definitely meet specified standards for impact (crash) protection and retention system strength and, afterwards, identifying those which definitely have ceased to meet those standards.
The Snell Foundation urges that protective helmets be required for all individuals participating in supervised racing events and encourages the general public to wear helmets which meet appropriate performance standards.
This 2015 Standard establishes performance characteristics suitable for motorcycling and for use with other open motorized vehicles in which the driver and passengers may not be enclosed such as boats, motorized carts, all-terrain vehicles and snowmobiles.
This Standard does not establish construction and material specifications. The Foundation does not recommend specific materials or designs.
Manufacturers voluntarily submit helmets to be tested to this Standard and if the submitted helmets pass, a certification is issued.
The Foundation will make available the identity of those products which have been Snell certified but will not attempt to rank those products according to performance nor to any other criteria.
Neither does the Foundation distinguish between the needs of participants in competitive events and those of the general public.
All of the requirements described herein, including both initial certification and random sample testing, are an integral part of this Standard.
No helmet can satisfy the Standard unless it is subject to both certification and random sample testing by the Foundation.
Snell certification for protective headgear requires a specific contractual agreement between the primary headgear manufacturer and the Foundation.
Certification procedures may be obtained upon application to the Foundation.
Snell Memorial Foundation is a registered certification mark and M2015 is a certification mark of the Snell Memorial Foundation.
Introduction
This Standard addresses the problem of protecting the head from direct impact with surfaces or objects that might be encountered in a motorcycling accident.
The Standard prescribes direct measures of several factors bearing on a helmet’s ability to protect the head as well as its general serviceability as motorcyclist headgear.
Thus, this Standard is directed towards the kinds of performance bearing on head protection that may not readily be discernable by even knowledgeable consumers at the time of purchase.
Some of these performance requirements have been expressed in terms of limitations on the various components and features of the single general helmet configuration currently available.
These expressions have been used only for the sake of clarity and should not be misinterpreted as requiring specific configurations or materials.
As newer helmet technologies appear, these limitations will be re-examined and, perhaps, restated.
Parts of a Motorcycle Helmet
A motorcycle helmet consists generally of a rigid head covering and a retention system composed of flexible straps and hardware.
The rigid covering consists of a strong, stiff outer shell and a crushable liner. The stiff outer shell protects by its capacity to spread a concentrated load at its outer surface over a larger area of the liner and the wearer’s head.
The crushable liner protects the head from direct impact by its capacity to manage impact energy.
Since there is no certain way to anticipate the severity of a head impact or whether the impact surface will be such that it will spread the load over the helmet or concentrate it at a single point, the most generally effective helmet will combine the strongest, stiffest possible outer shell with a liner chosen to limit the peak deceleration of the wearer’s head to within tolerable limits.
Retention System and the Importance of Fit
The retention system holds the headgear in position throughout normal usage and especially during falls and accidents, ensuring that the helmet will be in place to manage a direct impact.
The M2015 Standard applies two different tests to the retention system.
The first of these tests for stability by fitting the headgear to a standard head form and then attempting to displace it by applying tangential shock loadings.
The second tests retention system strength by applying a shock load to the system components through a simulated chin.
The quality of the fit and the care taken with the adjustments are absolutely critical elements in these tests.
The manufacturer must provide suitable guidance so that the wearer will be able to select and adjust headgear to obtain the necessary quality of fit and positional stability.
The capacity for impact protection is determined by direct measurement of the shock delivered through the helmet to a head form when the helmeted head form is dropped in a specified manner onto any of three unyielding anvils.
Most motorcycle helmets are intended to accommodate a range of head sizes and shapes.
Various thicknesses of resilient padding are sometimes placed within otherwise identical helmets during production or during fitting to configure the helmet to several different ranges of head size.
This resilient padding does not significantly affect the way the helmet absorbs and attenuates impact and is not directly addressed in this Standard.
Penetration and External Forces
Sharp Points or Projectiles
The helmet must also resist penetration by sharp edged and pointed projections and projectiles.
This capacity is tested by placing the helmet on a head form and dropping a metal cone of specified mass and geometry onto the shell. The tip of this cone must not penetrate to the head form.
Liquids, Solvents and Chemicals
Similarly, the helmets must resist chemical attack by bodily fluids as well as solvents and chemicals associated with motorsports.
This capacity may be tested by applying a solvent mix before further conditioning and testing.
Facial Protection
Full face helmets — including “modular” or “flip-up” helmets — provide a measure of facial protection in addition to the impact protection generally sought.
The principle feature of these is a chin bar that extends forward to cover the jaw area converting the facial opening into a visual port.
Frequently, a face shield is also provided so that the wearer’s face is completely covered.
In traditional full face helmets, the chin bar is an integral, immovable part of the helmet structure. In “modular” or “flip-up” full face configurations, the chin bar may be released to pivot about a hinge up and away from the face enabling wearers to adjust eyeglasses, eat, drink or converse when not actually riding.
Although other helmets may be configured to allow the use of “bolt-on” chin bar elements, these helmets are not considered to be full face and are treated instead as open face configurations.
For full face helmets, this Standard tests the rigidity of the chin bar by dropping a weight onto it at a specified velocity so as to attempt to force the chin bar toward the interior of the helmet.
The chin bar must not deflect more than a specified amount.
Face Shield
If a face shield is provided with a full face helmet, then this face shield must resist penetration by small particles.
A sharp lead pellet of a specified weight is directed into the face shield at a specified velocity. The pellet must not penetrate into the helmet interior.
Emergency Helmet Removal
This Standard also includes a test intended to determine whether the headgear may be removed from an unconscious accident victim quickly, easily and reliably in spite of any damage the headgear might reasonably be expected to sustain.
Traditional helmet architectures have satisfied this requirement so readily that many Standards including previous Snell Foundation Standards have not mentioned it.
Even so, it is unthinkable that a headgear might protect its wearer in an accident only to thwart attempts at rescue afterward.
Ventilation and Other Features
Inadequate ventilation may render a helmet un-wearable in hot climates, especially if the helmet is full faced.
But this Standard makes no direct demands on either the quantity or quality of air flow to the wearer.
Other general features of motorcycle helmets may include eyeshades and accommodations for goggles, and visibility enhancements such as bright colors and reflective surfaces.
These features all deal with matters of safety and comfort that are not directly addressed in this Standard but which merit the consideration of wearers as well as manufacturers.
Helmet Protective Capabilities
Although helmet use has been shown to reduce the risk of head injuries significantly, there are limits to a helmet’s protective capability.
No helmet can protect the wearer against all foreseeable accidents, therefore injury may occur in accidents which exceed the protective capability of any helmet including even those helmets meeting the requirements of this Standard.
A helmet’s protective capability may be exhausted while protecting the wearer in an accident. Helmets are constructed so that the energy of a blow is managed by the helmet, causing its partial destruction.
The damage may not be readily apparent and the Foundation strongly recommends that a helmet involved in an accident be returned to the manufacturer for complete inspection. If it is not possible to do so, the helmet should always be destroyed and replaced.
Finally, the protective capability may diminish over time.
Some helmets are made of materials which deteriorate with age and therefore have a limited life span.
At the present time, the Foundation recommends that motorcycle helmets be replaced after five (5) years, or less if the manufacturer so recommends.
CONSTRUCTION
A. General
The assembled helmet shall have smooth external and internal surfaces. Any feature projecting more than 7 mm beyond the outer surface must readily break away; all other projections on the outer surface shall be smoothly faired and offer minimal frictional resistance to tangential impact forces.
Rivets and similar projections into the helmet interior must offer no laceration or puncture hazard. Restraint clips may be used at the rear or on the side of the helmet.
The helmet shall provide as nearly uniform impact protection over the entire protected area as is possible.
If the absence of any detachable component of the helmet does not prevent its being worn, then this absence must not compromise either the retention system or the impact protection.
If any part of the helmet detaches during testing, it must offer no laceration or puncture hazard nor reduce the coverage of the head.
If the manufacturer provides add-ons such as visors, face shields and neck curtains with the helmet, these add-ons must not lessen the protective capability of the basic helmet nor reduce the visual field below standard requirements nor create a direct hazard for the wearer.
B. Shell
If rivets are used, the heads shall not have sharp edges and shall not project more than 2 mm from the outer surface of the helmet.
C. Materials
Ideally, materials used in the manufacture of the helmet should be of durable quality and not be harmed by exposure to sun, rain, dust, vibration, sweat or products applied to the skin or hair.
Similarly, the materials should not degrade due to temperature extremes likely to be encountered in routine storage or transportation.
Materials which are known to cause skin irritation or are conducive to disease shall not be used for the parts which contact the skin.
Materials which support the growth of fungi or algae shall not be used. Fabric lining or padding materials, if used, may be detachable for the purpose of washing so long as their absence does not degrade the protective capabilities of the helmet.
D. Finish
All edges of the helmet shall be smoothed and rounded with no metallic parts or other rigid projections on the inside of the shell that might injure the wearer’s head in the event of impact.
E. Retention System
The retention system shall be designed so as to discourage misuse.
That is, of all the ways in which the retention system might be used, the design use shall be the simplest and quickest to implement. Helmets shall not be fitted with “non-essential” features which, if misused, can degrade the performance.
Quick release buckles, if used, shall not be able to be released inadvertently. Fabric chinstraps, if used, shall not be secured to the shell by a bolt, pin or rivet passing through the fabric itself.
Although other alternatives may be proposed, the preferred method of attachment is that the strap be looped through and sewn about a metal hanger which can then be secured to the shell by bolt, rivet or other appropriate means.
F. Peripheral Vision
The helmet shall provide peripheral visual clearance as measured using a reference head form appropriate to the size of the helmet.
This peripheral vision includes a horizontal clearance of at least 210°, an upward clearance of at least 7° and a downward clearance of at least 30°.
However, this downward clearance makes specific allowance for breath deflectors. These clearances are described in terms of planes fixed in the reference head forms.
Some competitive applications may require helmets with more restricted visual fields.
When justified, special addenda to this Standard will define reduced visual fields, the procedures for determining whether a helmet satisfies the requirement and the additional labeling requirements warning that the headgear may be appropriate only for certain uses.
G. Sizing
The requirements of this standard are such that most helmets will perform optimally only when tested within a range of head circumferences.
Outside this range, helmets may still provide a measure of protection but they may not meet requirements for certification.
The manufacturer must specify this entire range when helmets are submitted for certification.
Later, when helmets are distributed for sale, every helmet shall include a permanent label indicating the range of head circumferences for which it is intended.
QUALIFICATIONS FOR CERTIFICATION
For qualification testing, helmets shall be in the same condition as those offered for sale. No helmet or component which has been subjected to any tests described in this Standard shall be offered for sale after testing.
At least five (5) and as many as seven (7) complete helmets must be submitted by the manufacturer for a certification test program for each distinct structural configuration of the models offered for sale.
All but one of these samples will be destroyed in testing; the untested sample shall be retained for comparison and reference.
If different fit pad configurations are planned in order to accommodate this head gear for different size ranges, five of the samples submitted must be configured for the largest size range.
If seven samples are considered necessary, the remaining two samples must be configured for the smallest intended size.
Additional samples representing different fit pad configurations may also be provided at the discretion of the submitter.
MODIFICATIONS
Cosmetic changes to certified headgear are permissible. Such changes are generally limited to marking or trimming the headgear with manufacturer approved paint or tape.
Otherwise, modifications to certified headgear effectively create new configurations which shall not have the confidence and certification of the Foundation until properly evaluated.
Manufacturers must not place the Foundation’s certification label in any modified headgear without the Foundation’s written authorization.
The Foundation recommends that helmet owners not modify or contract with someone else to modify their helmets.
Any structural modification may adversely affect a helmet’s protective capability. The Foundation’s certification and, quite likely, all manufacturer warranties apply to the headgear only in its as manufactured condition.
RANDOM SAMPLE TESTING
In addition to the certification testing, the Foundation will routinely obtain and test samples of previously certified models.
These samples will be selected from among those stocks intended for retail sale to consumers.
In this manner, the Foundation will attempt to ensure that the helmets made available to the public continue to meet the performance requirements of this Standard.
For those cases in which helmets are provided directly to users and do not pass through a normal sales distribution system, the Foundation will set up alternative procedures to monitor certified products.
Specifically, if helmets are provided directly to teams or individuals for use in events, the Foundation must have access to the helmets for spot checking and non-destructive evaluation.
LABELING AND MARKING
Each helmet shall have durable, visible and legible labeling identifying the manufacturer, the month and year of manufacture, the model and the size.
Labeling shall be un-coded and either in English or a language common to the area where the helmets are to be distributed.
The headgear shall also be labeled to the following effect:
- The Certification ID#: This number consists of two alpha characters, four numerics, a hyphen and two more numerics indicating the year in which the certification was awarded. This certification ID# is marked on the test reports, cover letter and the certificate awarded to the helmet maker shortly after the helmet met requirements, it identifies the tests and the archive samples on which the certification is based.
- No helmet can protect the wearer against all foreseeable impacts. However, for maximum protection, the helmet must be of good fit and the retention system must be securely fastened to retain the helmet. The helmet, when fitted and fastened, shall not be removed easily.
- This helmet is so constructed that the energy of an impact may be absorbed through its partial destruction, though damage may not be visible. If it suffers an impact, it must either be returned to the manufacturer for inspection or be destroyed and replaced.
- Intended for head circumferences from XX cm through YY cm.
If any of the helmet components are sensitive to common solvents, adhesives, paints or cleansers; the helmet must also bear labels to the following effect:
- This helmet can be seriously damaged by some common substances without visible damage. Apply only the following: (Recommended cleaning agents, paints, adhesives and the like) as appropriate.
If the helmet model was certified according to a special addendum to this standard, each helmet shall also include the warning labels required by that addendum.
The Certification ID# label requirement is intended to minimize confusion during standards enforcement.
It may be waived at the discretion of the Foundation if the manufacturer can demonstrate that existing brand and model labels will reasonably identify the unit sufficiently. Any such waiver must be obtained in writing.
Each helmet shall also include one of the Foundation’s serialized certification labels.
The Snell certification label shall be placed either inside or on the outside of the helmet, as appropriate, in such a way that it cannot be removed intact.
GRAPHIC
The registered trademark (certification label) of the Snell Memorial Foundation may be used by the manufacturer only under license from the Snell Memorial Foundation.
The specifics of licensure may be obtained from the Foundation.
MARKING AND LABELING OF CRITICAL COMPONENTS
If a helmet component may reasonably be replaced with an inappropriate substitute that might degrade wearer safety and performance in any of the tests called out in this standard, the manufacturer must mark those components so that users may avoid the purchase and use of inappropriate replacement parts.
In particular, face shields on full face helmets must be marked to identify the manufacturer and the month and year of manufacture.
HEAD FORMS
This standard invokes six standard head forms for helmet inspection, marking and testing. The geometry of these head forms is according to the definitions for the ‘A’, ‘C’, ‘E’, ‘J’, ‘M’, and ‘O’ head forms described in International Standards Organization (ISO) Draft Standard ISO DIS 6220-1983.
The impact mass specifications for the impact test phase are comparable to those in ECE 22-05 for these same head form designations.
ISO DIS 6220-1983 includes descriptions for half head forms suitable for guided fall impact testing or for full head forms such as those used in the positional stability tests.
Figures 1 and 2 depict the general shapes of the half head form configuration. The following table lists useful dimensions from the two references given above.
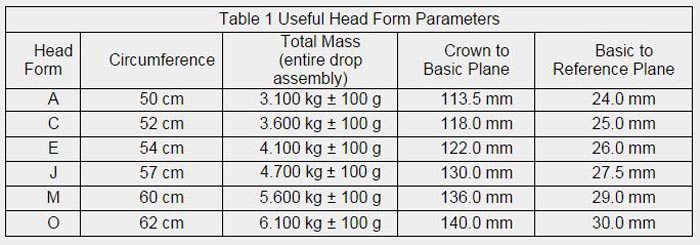
EXTENT OF PROTECTION
The extent of protection corresponds to that region of the head for which protection is sought. There are a number of planes fixed in the geometry of these head forms as shown in Figure 1:
Figure 1: ISO Head Form, ISO DIS 6220-1983
This description of the extent of protection uses the ISO definitions of the basic plane, the longitudinal plane, the transverse plane and the reference plane.
Other planes have also been defined strictly for convenience and clarity.
The basic plane corresponds to the anatomical plane (Frankfort plane) that includes the auditory meatuses and the inferior orbital rims.
The reference plane is above and parallel to the basic plane. The longitudinal or midsagittal plane is perpendicular to the basic plane and is the plane of symmetry dividing the right half of the head form from the left.
The transverse or coronal plane is perpendicular to both the longitudinal and basic planes. It corresponds to the anatomical plane that contains the two auditory meatuses and divides the front from the rear portions of the head.
These planes are all well known entities.
Several other planes, however, have proven useful. The S0 plane is parallel to the basic plane and lies above it at a distance determined by the size of the head form.
The S3 plane is parallel to the S0 plane and the basic plane and lies between them. The S4 plane is also parallel to these planes and lies below the basic plane.
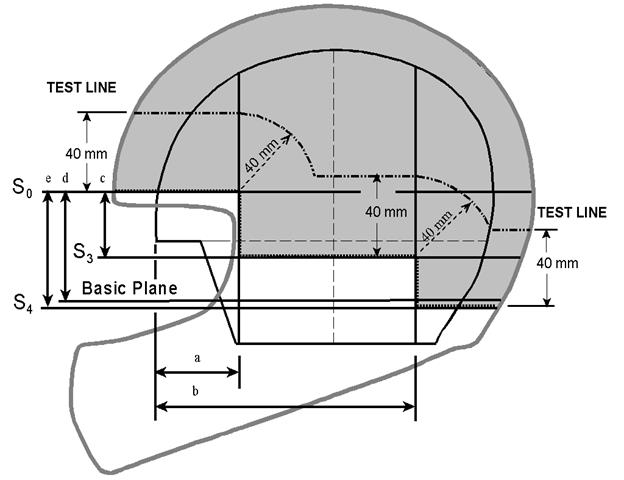

The rear plane divides the rear third of the head from the front two thirds.
It is parallel to the transverse plane and lies at a given distance behind the point where the reference plane and longitudinal planes intersect with the front surface of the head form.
The distance from this point, hereafter called the reference point, is determined by the size of the head form.
The fore plane is also parallel to the transverse plane. It lies behind the reference point at a distance determined by the size of the head form.
The extent of protection provided by the helmet must include the entire region above the S0 plane and forward of the fore plane, the entire region above the S3 plane and between the fore and rear planes and the entire region above the S4 plane and behind the rear plane.
Figure 2 and the associated table lay out these additional defined features and show the extent of protection and the test line.
TESTING
A. Inspection
Each helmet will be inspected for the required labels and for compliance with the general limitations made on structure.
Samples received for certification testing must incorporate all the critical component labels but other labeling is not necessary for evaluation.
Samples received for RST (enforcement) testing must have all the required labels.
Some helmets may incorporate innovations and other features not anticipated by this Standard but which raise concerns about the safety and effectiveness of the headgear.
These will be referred to members of the Foundation’s Board of Directors for evaluation.
Any feature deemed to reduce the protective capacity of the headgear, whether explicitly mentioned in this Standard or not, will be a cause for rejection.
B. Head Forms and Helmet Positioning
The determination of which head forms are appropriate to a helmet is based on the specified smallest and largest head circumferences for the helmet.
For samples submitted for certification, this specification must include the smallest and largest values of head circumference for every possible fit pad configuration of the helmet.
For helmets received for RST testing, the smallest and largest head circumferences will be taken directly from the helmet label.
If the smallest head circumference specified for the helmet is less than 50 cm, the A head form is the smallest appropriate.
Otherwise, the smallest appropriate head form for a particular helmet is the largest of the six head forms whose circumference is no greater than the manufacturer’s specified smallest circumference.
The largest appropriate head form is the largest of the six specified head forms whose circumference is no greater than the manufacturer’s specified largest circumference.
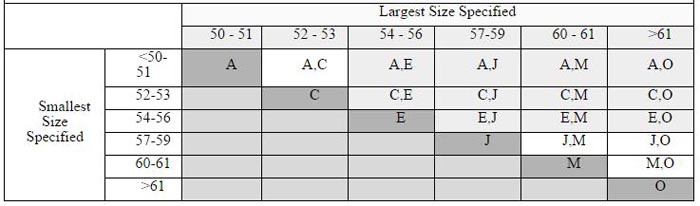
If the test samples are determined to be too small to accommodate the largest head form identified as appropriate, the next smaller head form shall be considered the largest appropriate.
If the samples are too small for even the smallest appropriate head form as indicated by the manufacture specification, the samples shall be rejected for certification.
The table shows which head forms will be used in certification testing for various head size specifications.
Since the largest head size should never be smaller than the smallest head size, most of the lower left region of the table is blank.
If the size specification corresponds to one of the gray cells along the table’s main diagonal, only a single test head form will be necessary and the manufacturer need only submit five samples identical samples configured with comfort padding for the largest intended head size for certification testing.
Otherwise, two more samples are required, identical to the first five in all respects except that the comfort padding must be configured for the smallest intended head size.
During testing, helmets will be positioned on the selected test head form according to the manufacturer’s specified helmet positioning indices.
If the manufacturer fails to provide positioning information with certification samples, the helmets will be positioned according to the best judgment of the authorized technical personnel.
If the helmets meet certification requirements, the helmet positioning indices will be those used in all future testing.
These helmet positioning indices represent distances on the front of the head form from the basic plane along the intersection with the longitudinal plane upward to the lower brow edge of the helmet.
Helmet positioning indices will be assigned for all head form sizes appropriate to the headgear.
Each headgear could conceivably require as many as six helmet positioning indices, one each for the ‘A’, ‘C’, ‘E’, ‘J’, ‘M’ and ‘O’ head forms.
C. Marking
The helmet is placed upon the largest appropriate ISO head form, positioned according to the apposite helmet positioning index and held in place with an applied force of 50 Newtons (11.25 lbs.).
The intersections of the shell with the various defined planes are then traced onto the outer surface of the helmet in the following manner:
- The level of the S0 plane is marked on that portion of the helmet in front of the fore plane.
- The level of the S3 plane is marked on that portion lying between the fore and rear planes.
- The level of the S4 plane is marked on that portion behind the rear plane.
- Finally, line segments along the fore plane are marked to join the S0 and S3 planes and, similarly, line segments along the rear plane are marked to join the S3 and S4 planes.
These lines enclose the top of the helmet and are the boundary of the required extent of protection.
However, it shall not be a cause for rejection if parts of this boundary fall below the edge of the helmet.
A test line shall be constructed within the extent of protection 40 mm from the closest point on the boundary as shown in Figure 2: Extent of Protection above.
If identical helmets are to be configured with different thicknesses of comfort padding to accommodate different ranges of head size, the required extent of protection marked on the test samples shall include the required extent of protection for each different configuration as marked on the largest head form appropriate for each.
That is, the helmet must meet all the requirements of this Standard in each of the intended configurations.
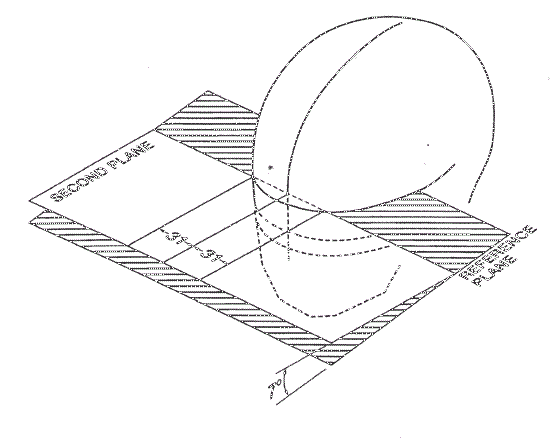
D. Peripheral Vision
The clearance for peripheral vision will be checked by placing the helmet on each appropriate ISO head form, positioning it according to the apposite helmet positioning index and holding it in place with a force of 50 Newtons.
The clearance must include the following solid angles to the front of the head form:
- The upward visual clearance.
- The lateral visual clearance.
- The downward visual clearance except for the breath deflector allowance.
Helmets certified to a special addendum to this standard and bearing the warning labels specified in the addendum will not be subjected to the following procedures and criteria for evaluating clearances for vision.
However, the procedures and criteria specified in the addendum will be applied instead.
The upward visual clearance is the solid angle bounded by the reference plane of the head form and a second plane tilted 7° up from the reference plane.
This second plane intersects the reference plane at two points on the front surface of the head form that are 31 mm to the right and left of the longitudinal plane as shown in Figure 3 (above).
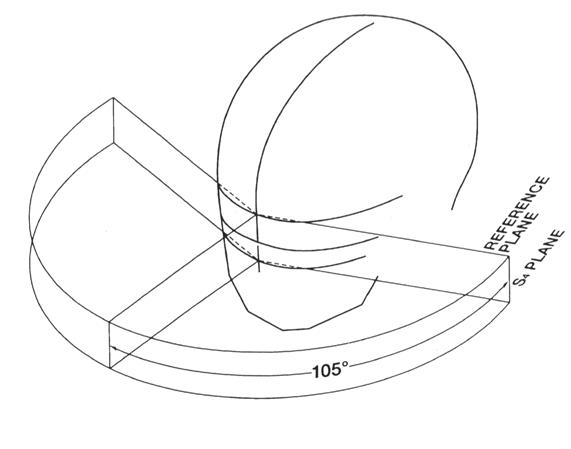
The lateral visual clearance, as shown in Figure 4 (above), is the solid angle bounded by the reference plane, the S4 plane and two more planes that are perpendicular to the reference plane and that contain the reference point on the front of the head form.
One of these two planes forms an angle of 105° with the longitudinal plane and lies to the left of the head form. The other forms the same angle to the right of the head form.
The downward visual clearance is the solid angle bounded by the basic plane of the head form and a second plane tilted 30° down from the basic plane that intersects it at two points on the front surface of the head form that are 31 mm to the right and left of the longitudinal plane as shown in Figure 5 (below).
However, intrusions into this downward clearance are permitted so long as the intrusions are within the breath deflector allowance.
The breath deflector allowance is shown in figure 6. It includes the region that is within 31 mm to the right and left of the longitudinal plane and that lies below the two planes that form 45º angles with the longitudinal plane and that intersect it at the level of the S4 plane.
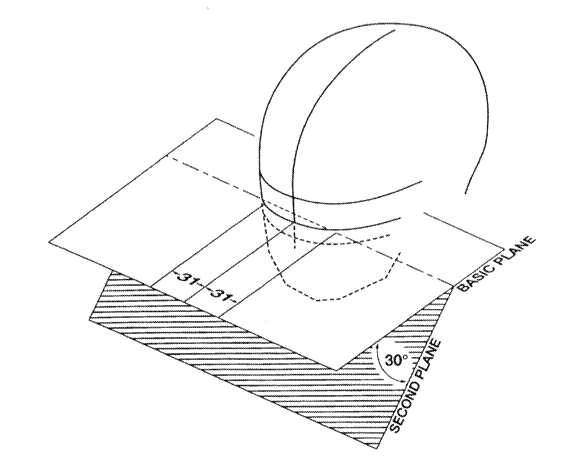
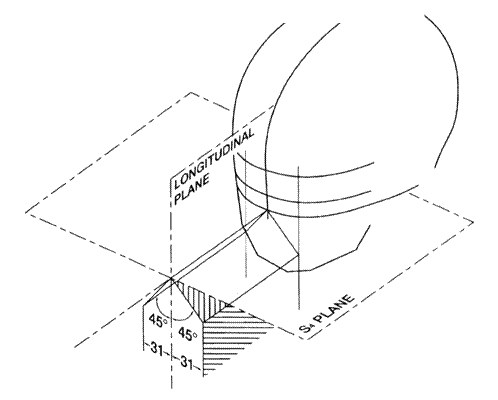
E. Performance Testing
The performance testing subjects helmets to a dynamic test of retention system strength, to a test for positional stability, to impact management tests, to helmet shell penetration tests, to a removability test, and to chin bar and face shield tests if appropriate.
These tests are conducted upon helmet samples kept under laboratory ambient temperature and humidity or that have been conditioned in one of three environments simulating some of the conditions in which the helmet might reasonably be expected to be used.
Prior to conditioning and testing, samples may be exposed to solvents common to motorsports which have been found to attack and degrade some helmet components.
In certification testing, four samples are required for testing on the largest appropriate head form.
The first of these is kept at laboratory ambient temperature and humidity and allowed to come to equilibrium. It is subjected first to the positional stability test and then to the impact management and other tests.
The second, third and fourth samples are conditioned hot, cold and wet, and subjected to the dynamic test of the retention system, the impact management test and the other tests.
If the smallest appropriate head form is not the same as the largest, two additional samples are required for testing on this head form.
The first of these will be allowed to stabilize at laboratory ambient temperature and humidity and then will be subjected to the test for positional stability.
This sample may then be conditioned hot or cold or kept at laboratory ambient for impact testing.
The second additional sample shall be tested in impact conditioned hot, cold or wet or kept at lab ambient according to the best judgment of the test personnel.
The selection of tests, conditioning and special conditioning is left to the discretion of the Foundation’s technical personnel.
However, for certification testing, each of the specified tests shall be applied to at least one sample.
Furthermore, it is expected that all testing will be conducted so as to exercise all the likely failure modes of the helmet.
E1. Conditioning for Testing
Test samples may be kept at laboratory ambient temperature and humidity or may be conditioned cold, hot or wet according to the specifications given below.
At the discretion of the Foundation’s technical personnel and at any point during the testing, a sample previously kept at ambient may be conditioned cold, hot or wet.
However, once a sample has been conditioned cold, hot or wet, the sample must be maintained in that condition throughout the rest of the testing.
The special solvent wipe conditioning described below may be applied to any sample at the discretion of the Foundation’s technical personnel.
a. Special Conditioning. Prior to any impact or retention system testing helmets may first be conditioned with a solvent mix of 50% toluene and 50% isooctane.
A cotton cloth or suitable substitute shall be soaked in the solvent and used as an applicator. The solvent will be applied to the shell first in an area within 5 mm of the chin strap attachments for not less than five (5) seconds on each side and then applied to the remainder of the shell for not less than ten (10) seconds.
At least thirty minutes shall elapse before further conditioning and testing.
b. Cold. The sample shall be conditioned by being exposed to a temperature of −20 ±2° C for a period of not less than four (4) hours, or more than twenty-four (24) hours.
c. Heat. The sample shall be conditioned by being exposed to a temperature of 50 ±2° C for a period of not less than four (4) hours, or more than twenty-four (24) hours.
d. Wet. The sample shall be conditioned by being continuously sprayed with water at a temperature of 25 ±5° C for a period of not less than four (4) hours, or more than twenty-four (24) hours.
This spray shall be directed at the helmet’s external surfaces. The helmet shall not be subjected to total immersion.
All testing of these hot, cold and wet helmets shall begin within two (2) minutes from the time of removal from the conditioning apparatus. The samples shall be returned to the conditioning apparatus between tests.
E2. Positional Stability (Roll-Off)
The test for positional stability shall only be applied to samples kept at ambient laboratory temperature and humidity.
The helmet shall not have been subjected to any prior performance testing.
The helmet shall be tested on the smallest appropriate standard full-face head form.
The head form shall be supported on a stand so that its vertical axis points downward at an angle of 135° to the direction of gravity.
The head form shall be oriented face down. The helmet shall be placed on the head form and adjusted to obtain the best configuration of the retention system.
An inelastic strap shall be hooked to the edge of the helmet at the rear centerline and brought forward so that its free end hangs downward across the top of the helmet.
An inertial hammer shall be suspended from the free end of the strap. This inertial hammer shall enable a 4.0 kg ±50 g mass to be dropped through a 0.6 m guided fall in order to deliver an abrupt shock load to the headgear.
The shock load will force the helmet to rotate forward on the head form. The helmet may be shifted but must remain on the head form.
The head form shall be repositioned so that it is facing upward but with the vertical axis still oriented downward at 135° to gravity.
The helmet shall be positioned and adjusted to obtain the best configuration of the retention system.
The strap/inertial hammer shall be hooked to the brow edge of the helmet at the center line so that the strap lies along the centerline and the hammer is suspended from the top of the helmet.
The shock weight shall be dropped through the 0.6 m guided fall delivering an abrupt shock load forcing the helmet to rotate rearward.
The helmet may be shifted but must remain on the head form.
The entire portion of the inertial hammer assembly that participates in the loading of the helmet shall be such that its mass is no more than 5.0 kg including the 4.0 kg shock mass.
E4.1 Impact Management Test Equipment
The dynamic test of the retention system may be applied to any sample either kept at ambient temperature and humidity or conditioned hot, cold or wet.
This test may be performed before, after, or between any of the other procedures in the test sequence.
However, the retention test shall not be valid if an integral chin bar has been removed from a full face helmet.
The helmet shall be supported on its lower shell edge in such a manner that the chin strap may be fastened under a device whose upper end approximates the contour of the bony structure of the jaw. The device will then be given a mechanical pre-load followed by a dynamic loading.
The retention system fails if it cannot support the mechanical loads or if the maximum deflection during the dynamic load exceeds 30 mm.
The retention system also fails if it cannot be easily and quickly unfastened after testing.
If the technician determines that the helmet cannot be adequately supported on its lower shell edge, at his discretion, he or she may support the helmet on a head form for this test.
a. This chinstrap loading device shall consist of a simulated jaw and accommodations for the pre-load and dynamic load.
The jaw portion shall consist of two metal bars or rollers, each one 12.7 ±0.5 mm in diameter, separated by 76 ±0.5 mm on center. The mass of this device shall not exceed 6.0 kg.
b. A pre-load shall be applied for at least 60 seconds.
This pre-load shall consist of the mass of the chin strap loading device, static load of 23 kg and the shock load of 38 kg ±500g which will total 61 kg ±500 g.
c. Raise the 38 kg ±500 g mass which will then be dropped in a vertical guided fall through a distance of 120 mm to load the retaining system abruptly; the shock load of 38 kg mass and static load of 23 kg mass shall not be additive.
In order to protect the test mechanism, the impact of the 38 kg mass may be cushioned with a 00-93 durometer rubber pad 150 mm in diameter by 6½ mm thick, or its equivalent.
E4. Impact Management Tests
The impact management tests may be performed on samples kept at ambient temperature and humidity or conditioned hot, cold or wet.
The sample shall not have been subjected to the shell penetration test beforehand.
These tests involve a series of controlled impacts in which the helmet is positioned on a test head form.
The helmeted head form is then dropped in guided falls onto specified test anvils. The impact site and the impact energy must meet certain requirements in order for the tests to be valid.
If the sample is so constructed that it interferes with the test equipment preventing impacts at sites within the test line, then, at the discretion of the Foundation’s technical personnel, parts of the helmet may be cut away to facilitate testing.
Every reasonable effort to minimize such cutting will be made. However, there shall be no relaxation of the impact levels or of the test criteria.
Certain tests shall not be valid when performed on samples that have been cut for impact testing: the dynamic strength of retention system test of section E3., the positional stability test of section E2., the chin bar test of section E5. and the removability test of section E8.
(Flip-up Helmets) Special considerations apply when the helmet is a “flip-up” model, that is: configured with a chin bar that pivots up and away from the face of the wearer.
For the first three impacts on any flip-up sample, the impact tests will be performed with the chin bar locked in the closed position.
In these tests the chin bar must not release and “flip-up” inadvertently. In certification testing, the tests will be structured so as to investigate performance in frontal followed by lateral impact.
E4.1 Impact Management Test Equipment
The test equipment shall consist of at least the following items:
a. The smallest and largest of the head forms appropriate for the helmet sample.
This head form shall be of rigid, low resonance metal such as magnesium alloy and shall conform to the ‘A’, ‘C’, ‘E’, ‘J’, ‘M’ or ‘O’ geometries specified in ISO DIS 6220‑1983.
b. A ball‑arm/collar assembly which is fitted to a socket machined into the base of the head form.
The ball/socket configuration shall be such that the geometrical center of the ball is located on the central vertical axis of the head form 12.7 mm above the reference plane as described in ISO DIS 6220-1983.
The ball-arm/collar assembly shall also include a uniaxial accelerometer fixed firmly into the ball.
c. A head form support assembly rigidly attached to the ball-arm.
This support assembly shall be such that it and consequently the head form may be guided in a vertical drop.
The mass of this support assembly shall not exceed 1.2 kg.
The total mass of the head form plus ball-arm/collar assembly plus head form support assembly shall be within 100 grams of:
- 3.1 kg for the ISO A head form;
- 3.6 kg for the ISO C head form;
- 4.1 kg for the ISO E head form;
- 4.7 kg for the ISO J head form;
- 5.6 kg for the ISO M head form;
- 6.1 kg for the ISO O head form.
d. A guidance system such that the head form/support assembly is guided in a vertical drop onto a test anvil.
This guidance system may consist of two or more wires or one or more rails. The head form/support – guidance system – test anvil alignment shall be such that:
d1. The drop trajectory shall be a straight line within 3° of vertical and within 5° of the sensitive axis of the uniaxial accelerometer.
d2. The line parallel to the drop trajectory and passing through the center of the head form ball-socket shall pass within 5 mm of the center of the test anvil, within 10 mm of the center of gravity of the head form/support assembly, and within 5 mm of the sensitive element of the uniaxial accelerometer.
e. A rigid anvil mount consisting of a solid mass of at least 500 kg. The upper surface of the anvil mount shall consist of a steel plate with a minimum thickness of 12 mm and a minimum surface area of 0.10 m².
f. Three test anvils: flat, hemispherical and edge.
f1. The flat anvil shall have a minimum surface area of 0.0127 m², e.g. 127 mm diameter face.
When fixed in position on the anvil mount, the surface shall be perpendicular to the head form trajectory.
f2. The hemispherical anvil shall have a 48 ±0.5 mm radius.
f3. The edge anvil shall have a striking face 6.3 mm wide with a depth of at least 35 mm. The radius of the edges on the impact face shall not exceed 0.5 mm.
When in position, the striking face shall be perpendicular to the head form trajectory. The anvil shall be sufficiently long that the ends do not contact the helmet during impact.
g. A uniaxial accelerometer. The acceleration data channel must comply with SAE recommended practice J 211 requirements for channel class 1000 with the exception that the frequency response need not include the range from dc to 10 Hz which may not be obtainable using certain types of transducers.
h. A velocity measurement device which will yield the velocity of the head form/support assembly within the last 40 mm of travel before impact. The velocity measurement must be accurate to within ±1%.
E4.2 Test Definitions
a. The impact site refers to the portion of the helmet struck during an impact test.
It is defined as the point where a line passing through the center of the head form ball and the center of the anvil intersects the outer surface of the helmet at the instant the helmet first touches the anvil.
b. The impact velocity is the velocity of the head form/support assembly as measured within no more than 4 cm of the first contact between the helmet and the impact surface.
c. This standard specifies nominal impact velocities which must be adjusted in order to allow for deviations between the actual mass of the test head form assembly and the specified ideal value.
The actual test impact velocity shall be the specified nominal velocity multiplied by the square root of the value obtained by dividing the ideal head form assembly mass by the actual mass.
For example, if, for the ‘A’ head form, the mass of the head form plus ball-arm/collar and support assembly as in paragraph E4.1c masses 3.2 kg instead of the ideal mass of 3.1 kg, the test impact velocities shall be obtained by multiplying the nominal velocities by a factor of 0.984.
d. There are two levels of test: the first is the standard level used to identify those helmets which definitely meet this standard.
It is applied to samples submitted for certification testing and to those acquired for the Foundation’s random sample test (RST) program.
The second is the deviation level which is applied to samples acquired for second round RST procedures; that is, testing of samples of currently certified models for which previous samples have obtained failing results in RST testing.
Failure to meet test criteria at the deviation levels indicates that the sample definitely does not meet the requirements of the standard.
E4.3 Test Impacts
Test impact sites shall be on or above the test line. Rivets, vents and any other helmet feature within this region shall be valid test sites.
Each impact site will be subjected to a group of one or two impacts according to the anvil selected for that site.
The impact site for the first impact within in a group is the target for the successive impacts in the same group.
However, if an impact group is sited closer than 120 mm to any previous impact group, that later impact shall be declared invalid.
There is no restriction regarding test anvil selection. The impact velocities for each test impact depend on the type of test and on the head form designation. Second impacts do not apply to helmets in tests against the edge anvil.
The technician may select either the largest or smallest appropriate head form for any particular group of impacts.
In all cases the technician may impact any site on the helmet surface on or within the test lines as drawn for any of the head forms considered appropriate for that helmet.
The nominal impact velocities are listed in the following table:
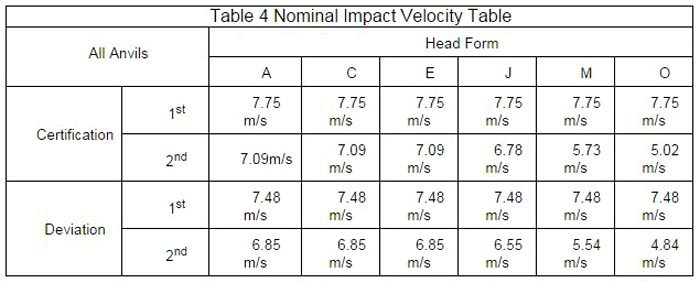
a. Each site tested against the flat anvil shall be tested according to the values in the impact velocity table adjusted for the mass of the head form assembly.
b. Each site tested against the hemispherical anvil shall be tested according to the values in the impact velocity table adjusted for the mass of the head form assembly.
c. Each site tested against the edge anvil shall be tested according to the values in the impact velocity table adjusted for the mass of the head form assembly. No helmet shall be subjected to the second impact for this anvil.
d. If the impact velocity for any test impact exceeds the specified mass adjusted velocity by more than 1.5%, that impact shall be declared invalid.
Please Note: The impacts described above are based on specific velocities and not prescribed drop heights.
To attain the proper velocity for an impact, it is likely that the drop height will need to be adjusted to compensate for frictions inherent in most mechanical helmet testing systems.
Height adjustments for these frictions should not account for more than 10% of the total drop height.
Also, the 1.5% margin allowed for impact velocity reflects the uncertainties expected even for well maintained drop equipment.
It is expected that drop heights will always be selected to produce, as closely as possible, the precise impact velocity as called out in the standards and adjusted for head form assembly drop mass.

E4.4 Impact Test Interpretation
The peak acceleration of the head form shall not exceed the values in the table above depending on the head form.
The helmet’s protective structures shall not break apart throughout the testing.
If the Foundation’s technical personnel conclude that fracture of the helmet shell, impact liner, retention system or other components could reasonably imply an undue laceration hazard either from the impact surface or from the helmet itself, the sample shall be considered to have failed.
(Flip-up Helmets) A flip-up configuration helmet sample tested with the chin bar closure locked at the outset of the any of the first three impacts performed upon it in testing and which “flips-up” inadvertently as a result of a valid test will also be deemed to have failed.
In most cases, each helmet must not “flip-up” as a result of two impacts applied to the first site tested and the first of the two impacts at the second site.
If, in certification testing, a sample is found to meet all the test criteria but any two of the impacts were at less than 98.5% of the specified impact velocity as adjusted for drop assembly mass, the testing for that sample shall be declared inconclusive and must be repeated.
Similarly, if there are two instances where an impact falls beyond 10 mm from the first impacts in its group, the testing for the sample shall be declared inconclusive and must be repeated.
Finally, if an invalid impact produces a peak acceleration exceeding the test criterion, the testing for the sample shall be declared inconclusive and must be repeated.
The impact test procedures leave considerable latitude to the helmet tester regarding site and anvil selection.
It is expected that the tester will orchestrate each standard test series in order to investigate potential weaknesses and to exercise each likely failure mode and will conduct deviation level testing to exercise the failure modes identified previously.
If at the end of a certification test series, the Foundation’s technical personnel conclude that the results obtained in valid impacts are not sufficient to determine whether the helmet model meets the performance requirements of this standard, additional samples may be conditioned and tested.
It is expected that all samples submitted will meet all the test requirements.
E5. Chin Bar Test
The chin bar test applies to full face helmets only. At least one helmet in each certification series shall be tested.
The helmet shall be firmly mounted on a rigid base so that the chin bar faces up and the reference plane is at 65 ±5° from horizontal.
A mass of 5 ±0.2 kg with a flat striking face of 0.01 m² minimum area shall be dropped in a guided fall so as to strike the central portion of the chin bar with an impact velocity of 3.5 ±0.2 m/sec.
The maximum downward deflection of the chin bar must not exceed 60 mm nor shall any component fail so as to cause a potential injury to the wearer.
E6. Shell Penetration Test
The shell penetration test may be applied to helmets kept at laboratory ambient temperature and humidity or helmets conditioned hot, cold or wet.
At least one helmet sample shall be tested in shell penetration.
The complete helmet shall be placed on a rigidly mounted head form. The test head form for the penetration test need not be the standard ISO head form shape used in the impact testing and helmet marking.
It is expected only that the device used will provide reasonable support for the helmet and conformance with the interior of the helmet immediately beneath the site of the penetration test. If the helmet contains a sling or some other adjustable sizing component, it shall be relaxed to its most extendable position.
The penetration test striker shall have a mass of 3 kg ±50 g and the point of the striker shall be a cone with an included angle of 60º ±0.5º and an altitude of 38 ±0.38 mm.
The striking tip shall have a hardness of 60 Rockwell (scale C ±3 points) and a radius of 0.5 ±0.1 mm.
The region of the support head form directly beneath the striker tip shall be wax or soft plastic so and covered with a thin tell-tale of paper, foil, tape or some similar material.
The striker shall be dropped to strike the surface of the helmet shell at a velocity of 7.45 ±0.15 meters per second as measured when the striker is no more than 4 centimeters away from contact with the helmet.
The helmet may be oriented on the support head form so that the test striker is directed at any site on or above the test line but the penetration test site must be at least 7.5 cm removed from the center of any impact test site or any other penetration test site.
At the test technician’s discretion, samples may be tested at more than one site on the shell.
For all penetration tests performed, the test striker must not penetrate through the helmet wall so as to put a hole in the tell-tale between the helmet and the support head form.
E7. Face Shield Penetration Test
If a face shield is provided with a full face helmet, this face shield shall be tested for penetration resistance in the following manner:
The face shield shall be tested on the appropriate helmet, correctly deployed across the facial opening and under laboratory ambient conditions.
A soft lead pellet weighing 1 ±0.1 g with a diameter of 5.5 ±0.1 mm and traveling at a velocity of 500 ±20 km per hour shall strike the face shield normal to the surface.
The face shield shall be tested in at least three different locations: the center line and 80 ±5 mm to either side of the center line. The pellet must not penetrate to the interior of the helmet.
E8. Removability
The helmet removability test determines whether the helmet can be removed from an unconscious victim without resorting to any buckles, clasps or other mechanisms which may be rendered non-functional by impact stresses.
The helmet is placed on the largest appropriate complete ISO head form with all the closures and retention systems engaged.
A technician must remove the helmet from the head form using simple, common hand tools but without accessing any of the helmet mechanisms.
The hand tools for this test are limited to shears, simple edged tools and flat bladed screw drivers. The operation must not require more than thirty seconds.
E9. Post-testing Disassembly and Inspection
If a set of helmets is submitted for and passes certification testing, at least one of the tested samples shall be disassembled and inspected.
If the laboratory staff identifies any internal feature that is not plausible for inclusion in a production helmet, the model shall be rejected.
If an internal projection on the helmet shell is deemed to present an undue laceration or puncture hazard, the model shall be rejected.
In evaluating these internal projections, no allowance shall be made for liner thickness.
At the discretion of the technician, any helmet may be disassembled in order to check for internal projections, plausibility or for deviations from the originally certified configuration.
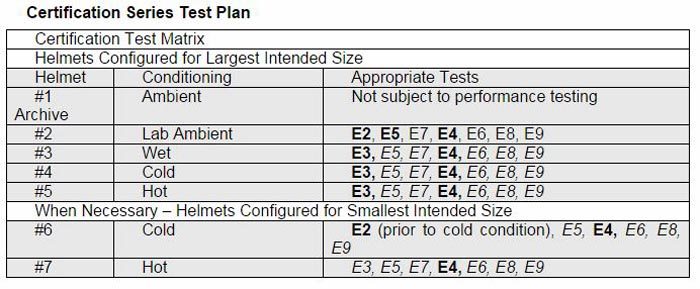
CERTIFICATION SERIES TEST PLAN
For a certification test series, it is expected that each test in this standard appropriate to the helmet configuration will be performed at least once.
It is also expected that the test technician will conduct the testing so as to obtain the most exhaustive evaluation possible of likely failure modes.
The table represents a typical certification test plan by sample number, conditioning and tests in order of application.
Bolding indicates that the particular test is routine for that sample; italics indicate the test is optional at the discretion of the test technician.
Please note: all the helmets submitted for certification testing are liable for inspection and the visual field check.
For more information, please visit the Snell Memorial Foundation website.
Publication Date: October 2014
Owner Comments and Feedback
See details on submitting comments.
No Comment